10+ Constant Pressure Techniques To Boost Efficiency

Constant pressure techniques are essential in various industries, including manufacturing, engineering, and construction, where maintaining a consistent pressure is crucial for efficient operation and safety. These techniques involve methods and technologies designed to regulate and sustain pressure within systems, ensuring optimal performance, reducing waste, and enhancing overall productivity. Understanding and implementing these techniques can significantly boost efficiency, leading to cost savings, improved product quality, and reduced environmental impact.
Introduction to Constant Pressure Techniques

Constant pressure techniques are fundamentally based on the principle of maintaining a stable pressure within a system, despite changes in external conditions or demand. This is achieved through a variety of methods, including the use of pressure regulators, valves, and sensors that monitor and adjust the system’s pressure in real-time. The application of these techniques can be seen in compressor systems, pneumatic systems, and hydraulic systems, among others. By ensuring that pressure remains constant, these techniques help in preventing pressure drops, leaks, and equipment failure, which can lead to downtime and increased maintenance costs.
Types of Constant Pressure Techniques
There are several types of constant pressure techniques, each designed for specific applications and industries. Some of the most common techniques include: - Pressure Regulation: This involves using devices that can adjust to changes in pressure, ensuring a constant output pressure despite fluctuations in input pressure. - Flow Control: By regulating the flow rate of fluids or gases, this technique helps in maintaining a constant pressure within the system. - Feedback Control Systems: These systems use sensors to monitor pressure and adjust the system accordingly to maintain a set point, providing real-time feedback and adjustments. - Proportional-Integral-Derivative (PID) Control: A sophisticated control method that uses a combination of proportional, integral, and derivative terms to adjust the system’s pressure, offering precise control and stability.
Technique | Description | Applications |
---|---|---|
Pressure Regulation | Maintaining constant output pressure | Compressor systems, pneumatic systems |
Flow Control | Regulating fluid or gas flow rates | Hydraulic systems, chemical processing |
Feedback Control Systems | Real-time pressure monitoring and adjustment | Aerospace, automotive manufacturing |
PID Control | Precise control using proportional, integral, and derivative terms | Process control, power generation |

Benefits of Constant Pressure Techniques
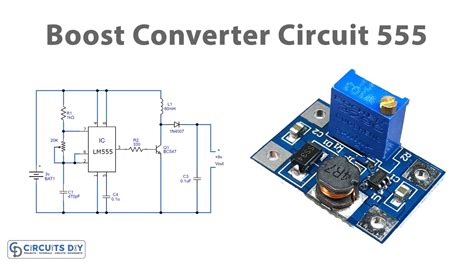
The implementation of constant pressure techniques offers numerous benefits across various industries. Some of the key advantages include: - Improved Efficiency: By maintaining optimal pressure, systems can operate at their best, leading to increased productivity and reduced energy consumption. - Enhanced Safety: Constant pressure techniques can help prevent accidents caused by pressure fluctuations, such as explosions or equipment damage. - Reduced Maintenance: With less strain on the system due to consistent pressure, the need for repairs and replacements decreases, leading to cost savings. - Increased Product Quality: In manufacturing, consistent pressure can lead to more uniform products, reducing defects and improving overall quality.
Case Studies and Examples
Several industries have seen significant improvements through the application of constant pressure techniques. For instance, in oil and gas, constant pressure systems are used to maintain consistent pressure in wells, improving extraction efficiency and safety. In manufacturing, constant pressure techniques are applied in injection molding to ensure uniform product quality. Additionally, in aerospace engineering, these techniques are critical for the operation of hydraulic systems in aircraft, where consistent pressure is essential for safety and performance.
- Oil and Gas: Improved extraction efficiency and safety through constant well pressure.
- Manufacturing: Enhanced product quality in injection molding processes.
- Aerospace: Critical for the safe and efficient operation of hydraulic systems in aircraft.
What are the primary benefits of implementing constant pressure techniques in industrial systems?
+The primary benefits include improved efficiency, enhanced safety, reduced maintenance, and increased product quality. These benefits are achieved through the consistent operation of systems at optimal pressure, leading to better performance, reduced downtime, and lower operational costs.
How do constant pressure techniques contribute to environmental sustainability?
+Constant pressure techniques contribute to environmental sustainability by reducing energy consumption, minimizing waste, and prolonging equipment lifespan. These outcomes lead to lower greenhouse gas emissions, less resource usage, and decreased pollution, aligning with sustainability goals and reducing the environmental footprint of industrial operations.
In conclusion, constant pressure techniques play a vital role in enhancing the efficiency, safety, and sustainability of various industrial operations. By understanding the principles and applications of these techniques, industries can adopt tailored solutions to improve their processes, reduce costs, and contribute to a more sustainable future. The continuous development and refinement of constant pressure technologies will remain crucial in meeting the evolving demands of industries and the environment.