Drill Press Drill

The drill press is a versatile and essential tool in many workshops and industries, offering precise and controlled drilling operations. Unlike handheld drills, drill presses provide a stable and rigid setup, allowing for accurate and repeatable drilling results. A drill press drill, specifically, refers to the drill bit or cutting tool used in conjunction with a drill press machine. These drills are designed to work seamlessly with the drill press's mechanical advantage, providing efficient and effective drilling capabilities.
Types of Drill Press Drills
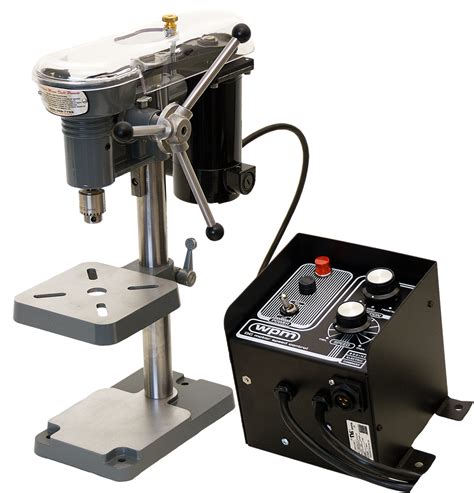
There are several types of drill press drills available, each catering to specific drilling applications and materials. Twist drills are the most common type, featuring a helical flute design that efficiently removes material and coolant. Step drills, on the other hand, have a unique stepped design, allowing for drilling of multiple hole sizes with a single drill bit. Counterbore drills are used for creating counterbores, which are recessed areas around a hole, often used for socket head cap screws. Additionally, spotting drills are used to create pilot holes for larger drill bits, ensuring accurate and centered drilling operations.
Drill Press Drill Materials and Coatings
Drill press drills are typically made from high-speed steel (HSS) or tungsten carbide, with some drills featuring coatings to enhance performance and extend tool life. Titanium nitride (TiN) coatings, for example, provide a hard and wear-resistant surface, reducing friction and increasing drill bit longevity. Aluminum oxide (Al2O3) coatings, on the other hand, offer excellent thermal resistance and are often used for drilling in high-temperature applications. Diamond-like carbon (DLC) coatings are also used, providing a low-friction surface and reducing drill bit wear.
Drill Press Drill Type | Material | Coating |
---|---|---|
Twist Drill | High-Speed Steel (HSS) | Titanium Nitride (TiN) |
Step Drill | Tungsten Carbide | Aluminum Oxide (Al2O3) |
Counterbore Drill | High-Speed Steel (HSS) | Diamond-Like Carbon (DLC) |
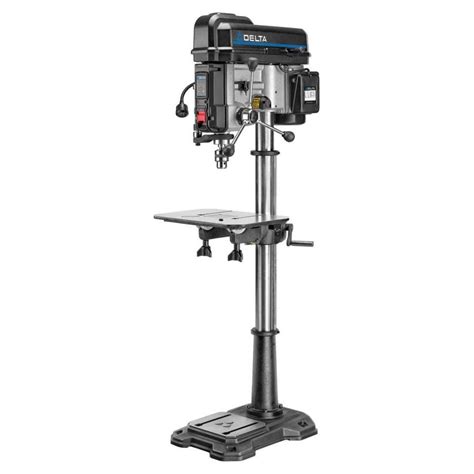
Drill Press Drill Performance and Optimization
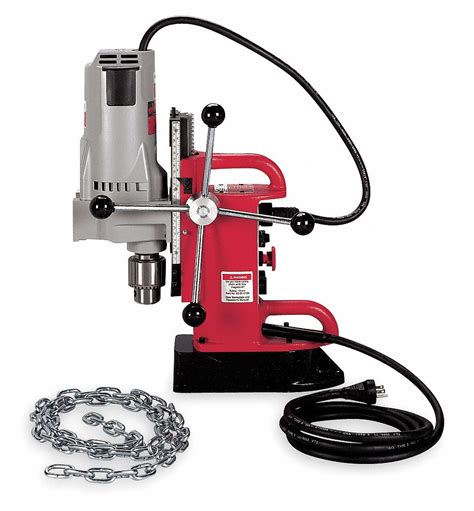
To optimize drill press drill performance, it’s crucial to maintain proper drill bit geometry, sharpening, and cooling. Drill bit angle and point geometry play a significant role in determining drilling efficiency and accuracy. A well-maintained drill bit, with a sharp cutting edge and proper flute design, can significantly reduce drilling time and improve hole quality. Additionally, coolant systems can be used to reduce heat buildup and prevent drill bit wear, ensuring prolonged tool life and optimal drilling performance.
Drill Press Drill Safety and Maintenance
Drill press drill safety and maintenance are critical aspects of ensuring optimal performance and preventing accidents. Proper drill bit storage and handling are essential to prevent damage and maintain drill bit integrity. Regular drill bit inspection and maintenance can help identify potential issues, such as wear or damage, and prevent drilling accidents. Furthermore, personal protective equipment (PPE), such as safety glasses and gloves, should always be worn when operating a drill press to prevent injury.
What is the primary advantage of using a drill press drill?
+The primary advantage of using a drill press drill is the ability to achieve precise and controlled drilling operations, resulting in accurate and repeatable drilling results.
What are the most common materials used for drill press drills?
+The most common materials used for drill press drills are high-speed steel (HSS) and tungsten carbide.
What is the purpose of a drill press drill coating?
+The purpose of a drill press drill coating is to enhance performance and extend tool life by reducing friction, wear, and heat buildup.