Grand Kaizen Guide: Transform Your Workflow
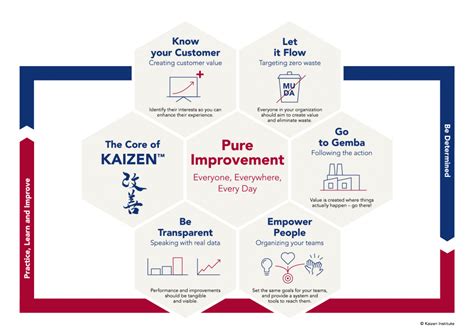
The concept of Kaizen, which originates from Japanese philosophy, emphasizes the importance of continuous improvement in all aspects of life. When applied to workflow management, Kaizen can lead to significant enhancements in productivity, efficiency, and overall job satisfaction. In this comprehensive guide, we will delve into the world of Kaizen, exploring its core principles, benefits, and practical implementation strategies to transform your workflow.
Understanding Kaizen and Its Core Principles
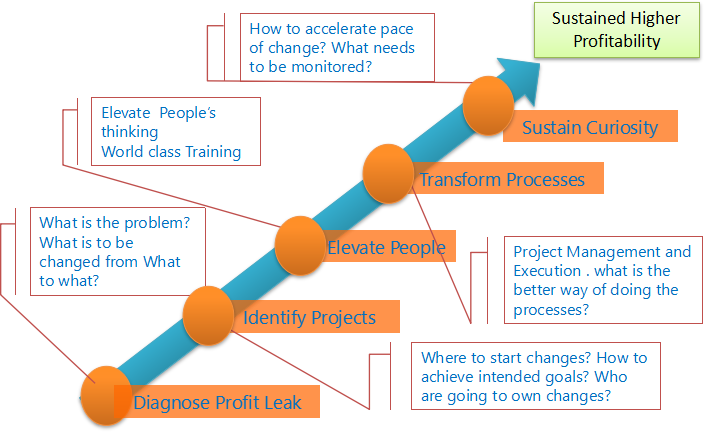
Kaizen is a Japanese term that roughly translates to “change for the better” or “continuous improvement.” It was first introduced in the post-World War II era as a means to enhance the country’s industrial capabilities. The philosophy of Kaizen is rooted in several key principles, including incremental improvement, employee involvement, and a focus on process over results. By embracing these principles, organizations can create a culture that values continuous learning, innovation, and progress.
Key Elements of Kaizen
There are several key elements that are essential to the successful implementation of Kaizen in any organization. These include:
- Identification of areas for improvement: This involves recognizing processes or workflows that are inefficient, wasteful, or in need of enhancement.
- Brainstorming and idea generation: Encouraging employees to contribute their thoughts and suggestions on how to improve identified areas.
- Implementation of changes: Putting the proposed improvements into action and monitoring their effectiveness.
- Evaluation and adjustment: Assessing the outcomes of the changes made and making further adjustments as necessary.
Benefits of Implementing Kaizen in Your Workflow

The integration of Kaizen principles into your workflow can yield numerous benefits, ranging from enhanced productivity and efficiency to improved employee morale and job satisfaction. Some of the most significant advantages include:
Reduced waste and costs: By identifying and eliminating unnecessary processes or steps, organizations can significantly reduce waste and lower operational costs.
Improved quality: Kaizen’s focus on continuous improvement leads to higher quality products or services, as processes are constantly being refined and perfected.
Increased employee engagement: When employees are involved in the improvement process, they are more likely to feel valued and engaged, leading to higher levels of productivity and job satisfaction.
Case Study: Implementing Kaizen in a Manufacturing Environment
A notable example of Kaizen’s success can be seen in the manufacturing sector. A company producing automotive parts implemented Kaizen principles by empowering its production line workers to identify inefficiencies and propose improvements. Through this initiative, the company was able to reduce production time by 30% and decrease defect rates by 25%, resulting in significant cost savings and improved product quality.
Implementation Phase | Outcomes |
---|---|
Pre-Kaizen Implementation | Production time: 10 hours per unit, Defect rate: 10% |
Post-Kaizen Implementation | Production time: 7 hours per unit, Defect rate: 7.5% |

Practical Strategies for Implementing Kaizen in Your Organization
Implementing Kaizen requires a structured approach that involves all members of the organization. Here are some practical strategies to consider:
Establish a Kaizen team: Form a cross-functional team responsible for overseeing the Kaizen process, providing training, and facilitating communication among employees.
Conduct regular Kaizen events: Organize workshops or meetings where employees can share ideas and work together on improvement projects.
Recognize and reward contributions: Incentivize employee participation by acknowledging and rewarding significant contributions to the Kaizen effort.
Challenges and Limitations of Kaizen Implementation
While Kaizen offers numerous benefits, its implementation is not without challenges. Common obstacles include cultural resistance to change, difficulty in sustaining momentum, and the need for significant upfront investment in training and resources. Overcoming these challenges requires strong leadership commitment, effective communication, and a well-planned implementation strategy.
What are the primary principles of Kaizen?
+The primary principles of Kaizen include incremental improvement, employee involvement, and a focus on process over results. These principles guide the continuous improvement efforts within an organization.
How can Kaizen improve workflow efficiency?
+Kaizen can improve workflow efficiency by identifying and eliminating unnecessary processes, reducing waste, and enhancing productivity through continuous improvement initiatives.
In conclusion, the Grand Kaizen Guide provides a comprehensive roadmap for transforming your workflow through the principles of continuous improvement. By understanding the core elements of Kaizen, recognizing its benefits, and implementing practical strategies, organizations can embark on a journey of enhancement and excellence, ultimately leading to improved productivity, efficiency, and job satisfaction.