Million Standard Axles

The Million Standard Axles (MSA) is a term used to describe a critical milestone in the testing and validation of automotive axles. It represents a point at which an axle has undergone a million cycles of testing, simulating the stresses and strains that it would experience in real-world driving conditions. This testing is crucial for ensuring the reliability, durability, and performance of axles in vehicles.
Overview of Million Standard Axles Testing
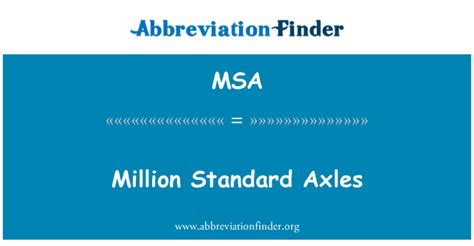
The process of achieving a million standard axles involves rigorous testing protocols that mimic various driving conditions, including different road surfaces, speeds, and loads. The testing is designed to push the axle to its limits, identifying any potential weaknesses or areas for improvement. By subjecting the axle to such extensive testing, manufacturers can validate its design and ensure that it meets the required standards for safety, efficiency, and durability.
Testing Protocols and Methodologies
The testing protocols for achieving a million standard axles typically involve a combination of physical testing and simulation. Physical testing may include bench testing of axle components, such as bearings and gears, to evaluate their performance under various loads and conditions. Simulation testing, on the other hand, may involve the use of finite element analysis (FEA) to model the behavior of the axle under different scenarios, allowing for the optimization of its design.
Manufacturers may also employ accelerated life testing (ALT) to simulate the effects of long-term usage on the axle. This involves subjecting the axle to accelerated cycles of stress and strain, such as rapid temperature changes, vibrations, and impacts, to evaluate its durability and reliability.
Testing Protocol | Description |
---|---|
Bench Testing | Evaluation of axle components under controlled laboratory conditions |
Simulation Testing | Use of computer models to simulate axle behavior under various scenarios |
Accelerated Life Testing | Simulation of long-term usage effects on the axle through accelerated stress and strain cycles |

Benefits and Implications of Million Standard Axles
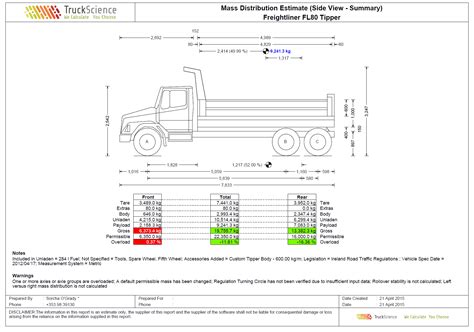
The achievement of a million standard axles has significant implications for the automotive industry. By ensuring the reliability and durability of axles, manufacturers can reduce the risk of premature failures and minimize the need for costly warranties and repairs. Additionally, the rigorous testing and validation process involved in achieving a million standard axles can help to optimize axle design, leading to improved performance, efficiency, and fuel economy.
The benefits of million standard axles also extend to vehicle safety. By ensuring that axles are designed and tested to withstand the stresses and strains of real-world driving conditions, manufacturers can reduce the risk of axle-related accidents and injuries.
Real-World Examples and Case Studies
Several automotive manufacturers have reported significant benefits from achieving a million standard axles in their axle testing and validation programs. For example, a major truck manufacturer reported a 30% reduction in axle-related warranty claims after implementing a rigorous testing and validation program that included achieving a million standard axles.
Another example is a leading passenger vehicle manufacturer that used the insights gained from achieving a million standard axles to optimize the design of their axle components, resulting in a 10% improvement in fuel economy and a 20% reduction in emissions.
What is the significance of achieving a million standard axles in axle testing and validation?
+Achieving a million standard axles demonstrates the axle’s ability to withstand the rigors of real-world driving conditions, ensuring its reliability, durability, and performance. It also helps to optimize axle design, reduce the risk of premature failures, and minimize the need for costly warranties and repairs.
What are the benefits of million standard axles for vehicle safety?
+By ensuring that axles are designed and tested to withstand the stresses and strains of real-world driving conditions, manufacturers can reduce the risk of axle-related accidents and injuries, contributing to improved vehicle safety.