Snout Armor Trim Tips: Boost Protection

Snout armor trim is a critical component in the protection of industrial and commercial equipment, particularly in environments where heavy wear and tear are common. The snout, being a vulnerable area, requires specialized armor to prevent damage from debris, abrasion, and impact. In this article, we will delve into the world of snout armor trim, exploring its importance, types, and tips for boosting protection.
Understanding Snout Armor Trim

Snout armor trim refers to the protective covering applied to the snout of equipment, such as conveyor belts, pumps, and valves. The primary purpose of snout armor trim is to shield the underlying components from damage caused by harsh operating conditions. Effective snout armor trim can significantly extend the lifespan of equipment, reduce maintenance costs, and minimize downtime. Abrasion-resistant materials, such as ceramics and urethane, are commonly used in snout armor trim due to their exceptional durability and resistance to wear.
Types of Snout Armor Trim
There are several types of snout armor trim available, each designed to cater to specific applications and environments. Ceramic snout armor trim is a popular choice for high-wear areas, offering excellent resistance to abrasion and corrosion. Urethane snout armor trim, on the other hand, provides flexibility and shock absorption, making it ideal for applications where impact is a concern. Other types of snout armor trim include metallic and composite materials, which offer a balance of strength, durability, and cost-effectiveness.
Snout Armor Trim Type | Key Characteristics | Applications |
---|---|---|
Ceramic | Abrasion-resistant, corrosion-resistant | High-wear areas, conveyor belts |
Urethane | Flexible, shock-absorbing | Impact-prone areas, pumps, valves |
Metallic | Strong, durable, cost-effective | General-purpose applications, equipment protection |
Composite | Balanced strength, durability, and cost | Various industrial and commercial applications |
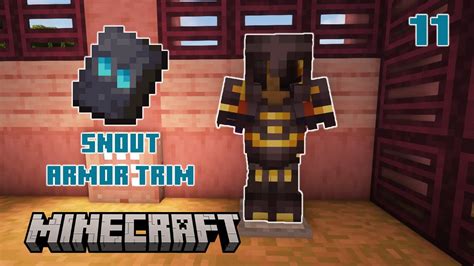
Boosting Protection with Snout Armor Trim Tips

To maximize the effectiveness of snout armor trim, several tips can be employed. Regular inspection and maintenance are crucial to identify and address potential issues before they become major problems. Proper installation is also vital, as incorrect fitting can compromise the integrity of the snout armor trim. Additionally, material selection should be based on the specific application and environment, taking into account factors such as temperature, abrasion, and impact resistance.
Snout Armor Trim Installation Best Practices
Proper installation of snout armor trim is critical to ensure optimal performance and protection. Follow manufacturer guidelines for installation, and use recommended materials and tools to prevent damage or compromise to the snout armor trim. Ensure a secure fit to prevent shifting or loosening of the trim during operation, and test the equipment after installation to verify proper function and protection.
- Follow manufacturer guidelines for installation
- Use recommended materials and tools
- Ensure a secure fit to prevent shifting or loosening
- Test the equipment after installation to verify proper function and protection
What is the primary purpose of snout armor trim?
+The primary purpose of snout armor trim is to shield the underlying components from damage caused by harsh operating conditions, such as debris, abrasion, and impact.
What types of materials are commonly used in snout armor trim?
+Abrasion-resistant materials, such as ceramics and urethane, are commonly used in snout armor trim due to their exceptional durability and resistance to wear.
How often should snout armor trim be inspected and maintained?
+Regular inspection and maintenance are crucial to identify and address potential issues before they become major problems. The frequency of inspection and maintenance depends on the specific application and environment.
In conclusion, snout armor trim plays a vital role in protecting industrial and commercial equipment from damage caused by harsh operating conditions. By understanding the importance of snout armor trim, selecting the right type of material, and following installation best practices, equipment owners and operators can boost protection and extend the lifespan of their equipment. Regular inspection and maintenance, proper installation, and material selection based on specific applications and environments are key to ensuring optimal performance and protection.